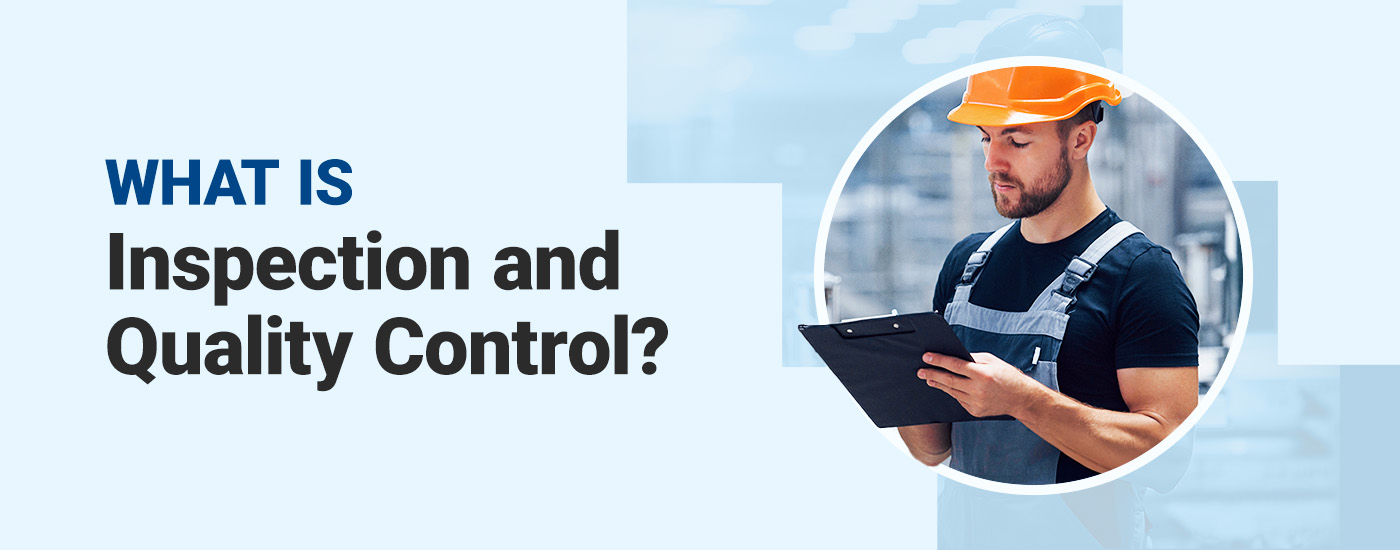
Companies rely on manufacturing to produce essential components and lifesaving machines for practically every commercial area. While manufacturing constantly produces new materials, how do companies ensure every client gets a product that performs as intended?
Quality control (QC) in manufacturing helps industries like aerospace, electronics, and medical devices confirm product effectiveness. A reliable inspection process can prevent expensive errors, support regulation compliance, and ensure safety. The more effective your inspection and quality control in manufacturing, the better the results for equipment manufacturers and their customers.
What Is Quality Control in Manufacturing?
Inspection and quality control is how a facility ensures products comply with any levied standards and meet all design requirements. Quality control includes everything from visual inspections to defect testing. Manufacturers will have contracted requirements that each product must meet to be sold — QC is how they make sure everything that comes off the line meets these requirements. The better the quality control process, the fewer errors, product escapes, and waste organizations have, and the higher their product reliability.
The Importance of Inspection and Quality Control in Manufacturing
Quality control is about more than finding defects. It’s designed to improve a company’s reputation, output, and overall processes. Anyone looking to maintain safety and follow standards set by industry-recognized organizations needs effective QC. Some of the main benefits of inspections include:
- Maintaining product consistency: QC inspections help with product consistency. Inspections ensure each product meets the same standards, maintaining precision and uniformity.
- Reducing costs: Catching defects early in the process reduces rework and waste, lowering production costs. Manufacturers can reduce their overall expenses by addressing issues during production instead of after customers receive products.
- Boosting customer satisfaction: Fewer defects means higher quality products and, therefore, happier customers. Consistent QC delivers reliable products, encouraging long-term brand loyalty and better relationships.
- Protecting brand reputation: Consistent QC also protects a manufacturer’s reputation. Reducing defects with QC prevents expensive recalls and brand perception damage.
- Ensuring and maintaining compliance: Many industries follow strict regulatory standards. QC helps them ensure products follow relevant regulations, avoid fines, maintain respective industry certifications, and combat other noncompliance issues.
3 Types of Quality Control
Since manufacturers need to check products throughout production, there are different types of quality inspections. Each production stage has its own checks to prevent poor-quality and noncompliant pieces from getting through.
1. Pre-Production Inspection
Raw materials parts need inspection before production begins. Flaws in the initial production setups and materials can compromise the entire product. The pre-production inspection stage assesses everything to ensure it meets the required starting specifications. This inspection helps detect potential issues that could affect quality so production begins on the right track.
2. During Production Inspection (DUPRO)
Once everything passes pre-production, manufacturing can start. DUPRO helps facilities catch defects as they happen instead of waiting until production is complete.
DUPRO means continuously monitoring pieces during production, also referred to as in-process inspections. Manufacturers can make real-time adjustments, ensuring everything coming off the line is in satisfactory condition. If there’s an issue with a batch, manufacturers can adjust to avoid waste and delays in every subsequent batch.
3. Pre-Shipment Inspection (PSI)
Finally, manufacturers conduct pre-shipment inspections (PSIs). PSIs are the last line of defense before goods go out to customers. This inspection ensures the finished products meet the required standards. Final product checks are especially critical for industries like aerospace and medical devices. After products go through the PSI, employees can complete packing or send goods back for repairs or replacements.
Quality Control Challenges
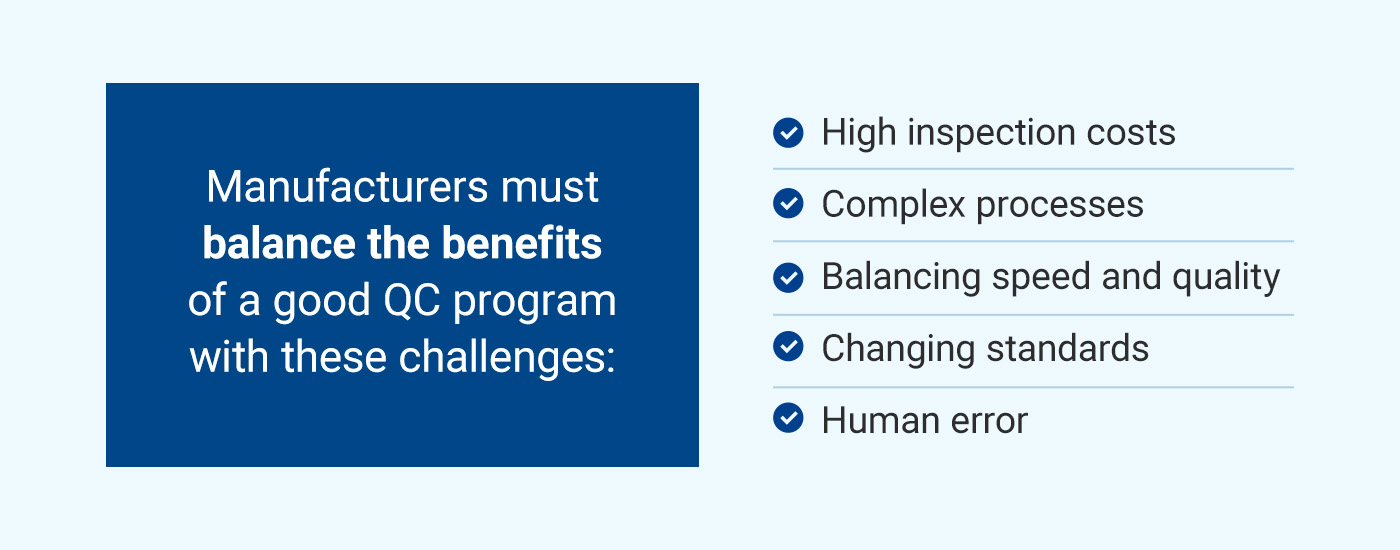
While QC is highly beneficial for manufacturers, it does present some challenges. Staying on top of various goods and their production can be time- and resource-intensive. More controls mean more expenses, which can affect profits. Manufacturers must balance the benefits of a good QC program with these challenges:
- High inspection costs: Implementing thorough QC measures involves investing in proper equipment, technology, and personnel. These costs can limit smaller manufacturers’ ability to perform comprehensive inspections.
- Complex processes: Manufacturing involves several stages, each with its own standards and equipment. Facilities must deploy various QC techniques and methods at different stages of the process order to achieve effectiveness. Therefore, a wide range of expertise is required to avoid production quality issues.
- Balancing speed and quality: Manufacturers also have to balance the demand for faster production with thorough QC. Rushed processes can reduce quality, and too low QC can affect the bottom line.
- Changing standards: Compliance standards are always changing. Sectors like biomedical see regular updates to keep pace with technology and changing science. Staying updated and compliant requires regular training and adaptation. Keeping on top of these standards can be resource-intensive and time-consuming.
- Human error: Even with automated QC and manufacturing, human error is always a challenge. Mistakes in inspection setups, data recording, or analysis can lead to missed defects.
How to Improve Quality Control in Manufacturing
The manufacturing world is no stranger to challenges. While QC presents unique hurdles, equipment manufacturers can work to improve their QC processes by:
- Investing in quality: Using advanced systems, like the VisionGauge® Digital Optical Comparator, improves your inspection accuracy. Advanced technology provides automated, high-resolution imaging and precise measurements for fewer errors and faster inspections.
- Standardizing procedures: Facilities need to create standardized inspection procedures to keep QC consistent and error-free. Clear standards help inspectors and operators maintain consistent results, even with automated processes.
- Using data: Modern inspection equipment collects data, analyzes trends, and suggests improvements. Manufacturers can harness this data to prevent future defects and adjust their QC approach.
- Training personnel: Skilled team members are critical for maintaining quality. Regularly train staff and keep them updated on the equipment and latest industry standards. Better training means better QC.
- Continuously improving: QC is always evolving. Manufacturers must regularly assess and refine their processes to meet changing requirements and customer demands.
Why Trust Us?
VISIONx, Inc. has earned a reputation for excellence as an industry leader in quality control solutions with our VisionGauge® Digital Optical Comparator and other advanced systems. Our solutions use patented, automated technologies to help manufacturers improve inspections.
We’re committed to providing efficient, reliable inspection tools so you can maintain a competitive edge in your industry. Our solutions are used across various sectors, helping companies meet rigorous standards without sacrificing productivity. Enjoy high-quality products and customization options to meet your specific needs.
Boost Quality Control in Manufacturing With VisionGauge®
Elevate your inspection accuracy and streamline QC processes with expert support. VisionGauge® systems provide your manufacturing facilities with reliable, advanced equipment for all your QC needs.
Let our systems and ongoing enhancements help you achieve top-tier quality control without sacrificing productivity. We’ll ensure every part meets your exact standards while simplifying compliance.
Discover how VisionGauge® systems can transform your inspection capabilities. Contact us today to learn more or to request a personalized consultation with our expert team!
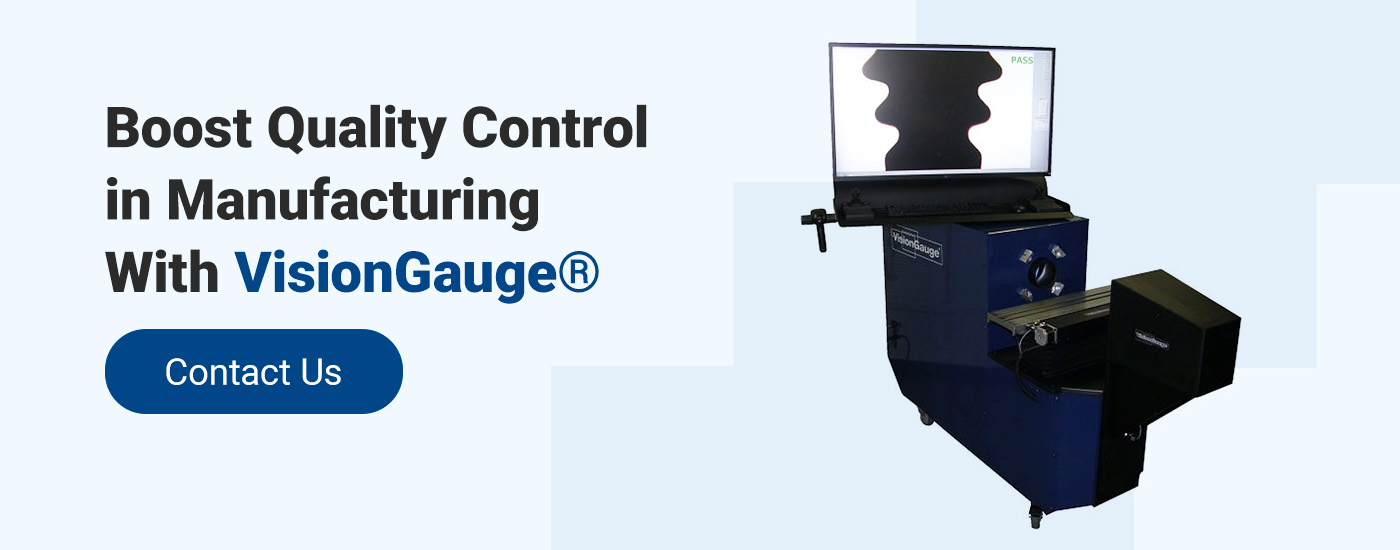
Linked Sources:
- https://www.nist.gov/about-nist
- https://www.iso.org/about
- https://www.visionxinc.com/digital-optical-comparators/applications/aerospace-and-aeronautics
- https://www.visionxinc.com/digital-optical-comparators/applications/medical-manufacturing
- https://www.visionxinc.com/digital-optical-comparators
- https://www.visionxinc.com/about-visionx/compliance-traceability-documentation
- https://www.visionxinc.com/digital-optical-comparators
- https://www.visionxinc.com/customized-inspection-and-measurement-systems
- https://www.visionxinc.com/contact-support