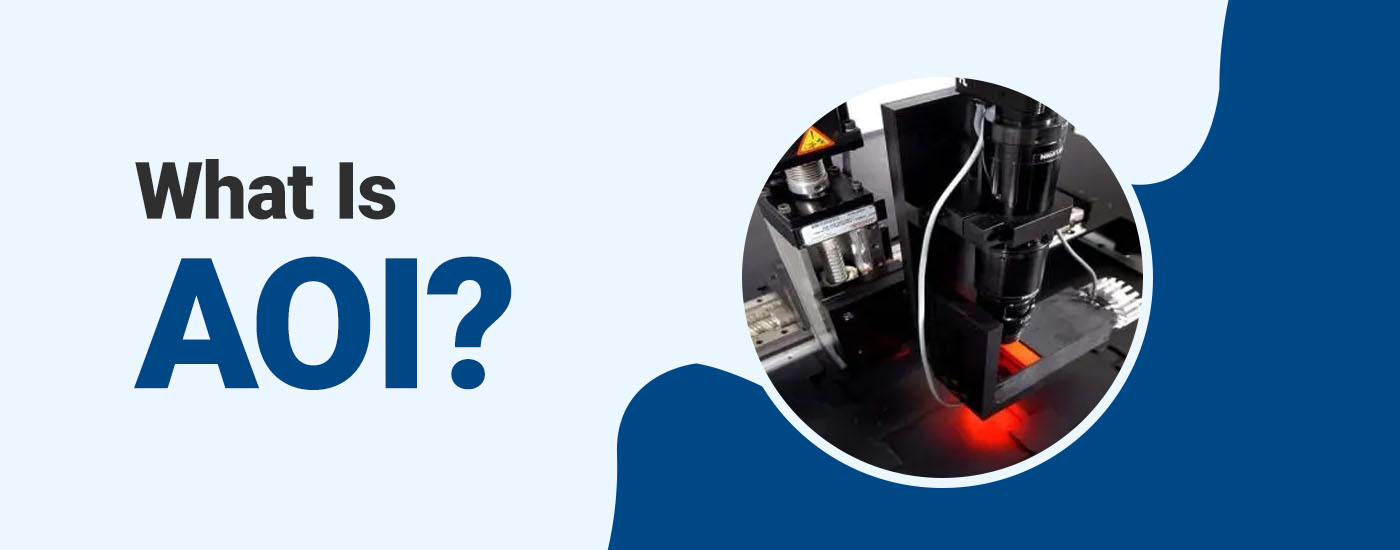
Automated optical inspection (AOI) technology is used in manufacturing processes to detect defects and ensure inspected products are of the highest quality. The system utilizes cameras and computer vision algorithms to inspect components, assemblies, printed circuit boards, and other parts for discrepancies in terms of soldering, component placement, and other manufacturing defects.
Optical inspections performed manually can miss minor imperfections as a result of human error. The precision and efficiency of AOI eliminate this concern, and when combined with automated reporting of results, it makes AOI an invaluable addition to any modern manufacturing facility. As a result, this technology has become an essential tool in enhancing quality control processes across a diverse range of industries, particularly in electronics manufacturing.
What Is an AOI System?
The quality of the images an AOI system can produce determines the accuracy of product inspections. There are three vital components that comprise an AOI system and facilitate its ability to detect product flaws:
- Light source: The light source illuminates inspected products. This component directly influences the quality and accuracy of image capture and defect detection. Appropriate lighting conditions enable the cameras to highlight features, detect subtle defects, and enhance contrast for clearer imaging. Various AOI systems use different types of light sources depending on the intended application. Most modern systems use LED arrays and halogen lamps. These provide consistent illumination for thorough examinations.
- Lenses: The lens directs the light reflected off the product into the camera sensor. AOI systems use premium-quality lenses to capture sharp images. A lens system can be adjusted to change the depth and field of view, making it possible to inspect different types and sizes of products.
- Camera: The third component is the digital camera that captures the product’s image. Different systems may use a standard 2D camera or a sensor that captures rotational images for a 360-degree view of the part.
Types of AOI
Optical inspection needs vary, so there are multiple types and configurations of AOI systems available.
Inline AOI
Inline AOI is a quality control process where the AOI system is integrated into the manufacturing line, allowing product inspections to occur in real time. With inline AOI, inspection times are limited because the evaluations must be completed as the products move through the production line.
Online AOI
Online AOI refers to inspection stations located within the manufacturing line but not directly integrated with it. Components are inspected as they move along the assembly line, but the inspection process may or may not halt the line if a defect is found. Online AOI systems are commonly used for inspecting randomly selected samples and are therefore ideal for high-speed production. Software like VisionGauge® OnLine provides additional tools and features to enhance online AOI effectiveness.
Offline AOI
Offline AOI systems inspect components and products outside the production line. This approach allows goods to be inspected in a separate, controlled environment. Choosing an offline AOI system often means slower output but enables more detailed and comprehensive inspections without time constraints.
2D AOI
The most common type of AOI system is two-dimensional AOI. These systems utilize 2D cameras to take photos of items for inspection and represent the most effective method for detecting surface-level defects. Incorrect or missing components, misalignments, and soldering defects are easily identifiable using this setup.
3D AOI
Three-dimensional AOI systems are a more advanced version of this technology. These scanners may produce a 360-degree rendering of the item, using sensors instead of cameras to create topological maps of the inspected components or products.
Benefits of AOI
Building an automated AOI system into a manufacturing line affords an operation numerous advantages:
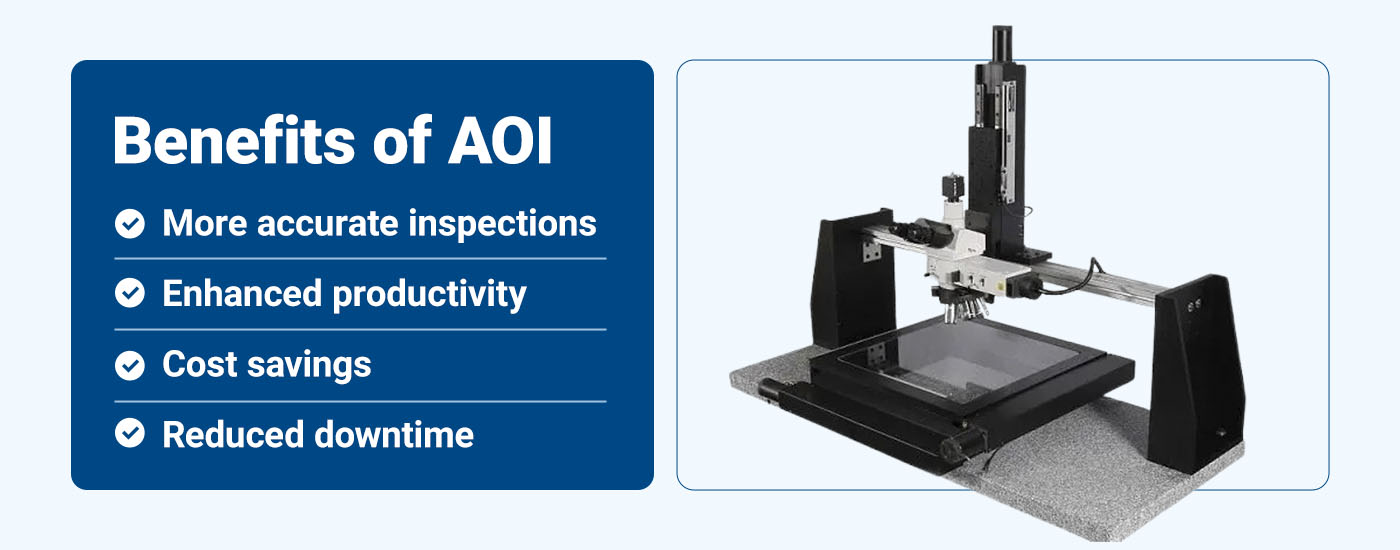
- More accurate inspections: Because AOI provides detailed images and scans of components, these systems can pick up the tiniest defects or deviations from production standards. This technology can perform ultraprecise measurements to confirm dimensional accuracy.
- Enhanced productivity: These machines can operate at high speeds, completing thousands of inspections per hour. AOI systems are valuable assets for high-volume manufacturing and production facilities.
- Cost savings: Manufacturers can reduce their production costs by finding defects early, allowing them to avoid unnecessary expenses like recalls or material waste. Using AOI equipment also has the potential to reduce customer complaints related to the release of defective goods.
- Reduced downtime: Utilizing an AOI system can significantly reduce overall production time, especially when replacing manual inspection as the chief source of quality control operations. Eliminating a potential bottleneck in quality assurance allows manufacturers to accelerate the flow of products to market.
Limitations of AOI
While AOI systems provide a lot of value, manufacturers do need to be aware of a few factors before they make the initial investment in this technology:
- Special setup requirements: Setting up and programming AOI equipment can be an intricate process requiring a specialist with in-depth knowledge and training. Because of the steep learning curve, it could be extremely challenging for a layperson to install and program this technology correctly.
- Difficulty in adapting to new versions: AOI systems are rigid, but line processes tend not to be. AOI is far less effective in situations that involve rapid product changes, as inconsistency in the scanned objects could make it difficult to identify defects correctly. An AOI system generally must know exactly what is working with and is looking for at all times.
- Programming demands: AOI equipment must be programmed on-site, and unless the programming is transferrable, it can only be done on one machine at a time. For larger setups, this could cause major delays, especially when frequent changes must be made.
- Inability to detect new issues: While AOI equipment can find a large variety of defects, it can only identify the defects it is instructed to find, such as dimensional errors or a flawed surface finish. Consequently, new, unexpected issues could pass through inspection undetected.
Due to the limitations of AOI technology, it is best suited for established products and manufacturing lines where any potential issues are already known and the design is unlikely to see frequent changes. In these scenarios, the speed and accuracy improvements it provides yield an excellent return on investment.
How to Integrate an AOI System Into a Production Line
Integrating an AOI system into a manufacturing process involves several key steps:
- Assess system requirements: Understanding the specific requirements of the production line is important. Consider the types of defects that need to be detected and the desired level of inspection accuracy.
- Select the right AOI system: Make sure the AOI system you choose aligns with the intended production line. Consider factors like whether you need 2D or 3D inspections and how quickly you need the products to move through the quality assurance phase.
- Prepare the production line: Ensure the production line is ready for AOI integration. Review the workflow and set up appropriate conveyor systems or interfaces to keep products moving seamlessly through the inspection station.
- Employee training: Provide training to employees and operators to ensure they know how to maintain the AOI system. You’ll also need to train personnel in interpreting and responding to inspection results.
Trust VisionGauge® With Your Production’s Integrity
VisionGauge® AOI systems feature advanced engineering to suit your production needs, whatever they may be. VisionGauge® machines provide you with a variety of manual or fully automatic inspections, precise part measurements, and excellent quality control, and we back them with exemplary application support. Our team specializes in creating powerful, intuitive technology to support production operations across diverse industries.
Contact us to find out more about what our products can do or explore our range online today.