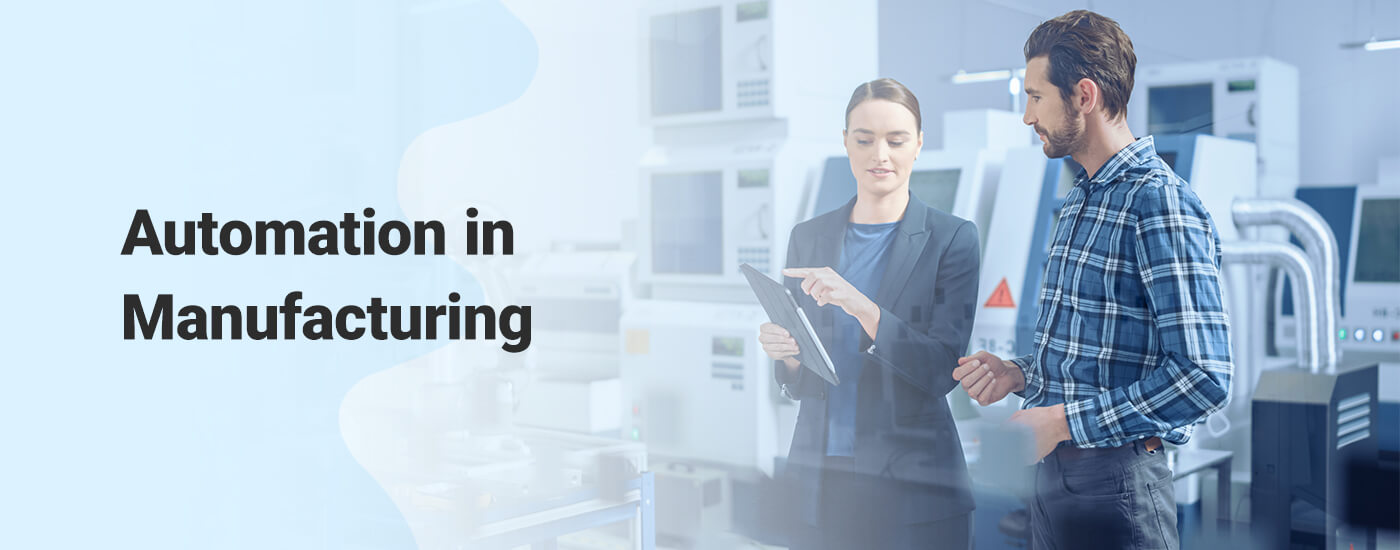
It’s no surprise that the global industrial automation market is expected to reach $430.9 billion by 2030. Automation is an increasingly popular engineering feat for more efficient labor, time and cost savings, increased safety protocols, and often better products overall. Discover the benefits of automation systems in various manufacturing industries.
What Is Automation in Manufacturing?
Manufacturing automation uses specialized equipment to streamline production assignments, systems, and processes. It’s incredibly helpful for repetitive tasks or those requiring high precision.
Manufacturing processes like assembling, inventory management, handling, processing, and quality inspection can all integrate automated technology. Automation in manufacturing aims to elevate capacity, lower operating costs, improve productivity, and enhance workplace safety measures.
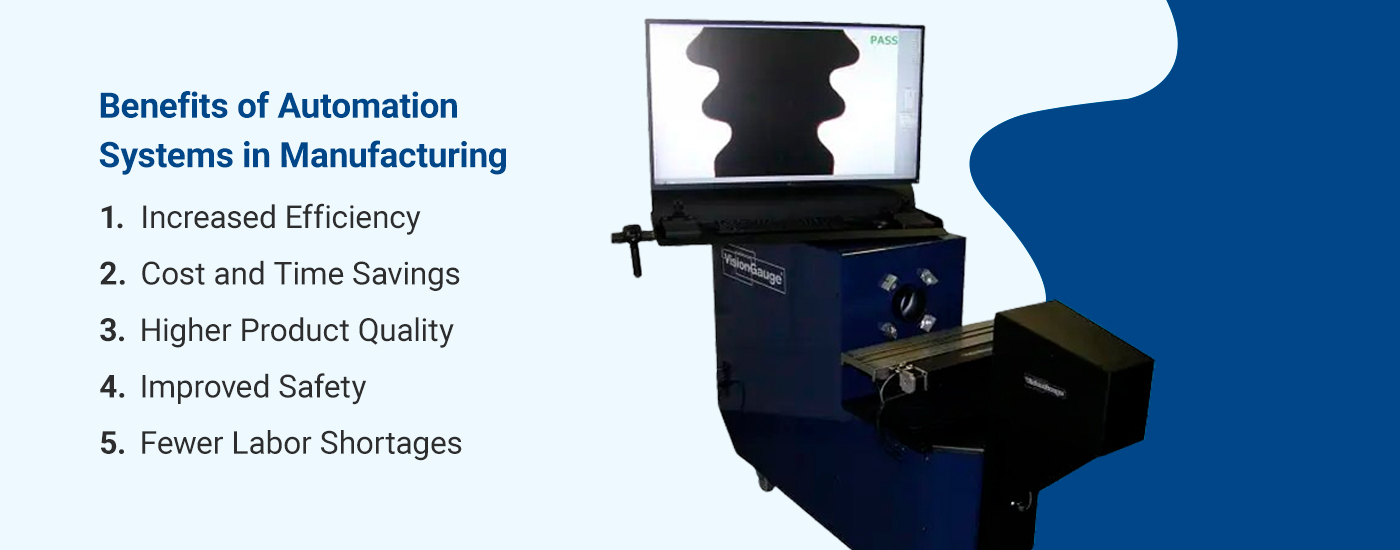
Benefits of Automation Systems in Manufacturing
Below are some advantages automation can provide for manufacturing.
1. Increased Efficiency
Automated machines can work unattended 24/7, maintaining the same speed and efficiency throughout. Advanced equipment, robotics, and sensors can oversee inventory, system maintenance, and quality checks on completed products. They can seamlessly disperse this data throughout the supply chain. This maximizes scheduling and planning, decision-making, and return on investment (ROI).
Automation can help your operations persist longer and boost productivity. You can generate new or more products without disrupting manufacturing. Additionally, this increased production speed gives companies higher responsiveness to market fluctuations, helping them stay ahead of competitors.
2. Cost and Time Savings
Many machines can perform the work of several people at a time with fewer defects, offering significant value and cost savings in the long run. Automated technology can also generate more products and complete inspections in less time. This increased production rate saves considerable amounts of valuable time.
3. Higher Product Quality
Machines can typically complete manufacturing processes with greater accuracy than human employees, all while ensuring the same product quality throughout. This allows for a lower error rate and overall better products. Standards can be stricter and products more competitive in the market.
4. Improved Safety
In 2022, the Occupational Safety and Health Administration (OSHA) cited over 22,000 U.S. workplace safety violations among its leading complaints, including citations in fall protection, hazard communication, respiratory protection, and other areas.
Reducing human error with automation can create a safer workplace, as it reduces repairs, recalls, and potentially severe injuries. Before advanced machinery, many manufacturing processes required employees to work for extended periods around various hazards, such as chemicals, electricity, machine guarding, equipment maintenance, and more.
Generally speaking, incidents like machine malfunctions and slipping or tripping on loose materials can be prevented with this technology. Automation helps keep workers away from dangerous substances or processes.
5. Fewer Labor Shortages
Automated machines can combat labor shortages and their resulting effects, as they’re less likely to be in low supply than human workers. Sufficient labor makes all the difference in a manufacturing company’s success.
Top Industries to Benefit From Inspection Automation
Automation is revolutionizing many industries, from retail and transportation to electronics. Below are merely a few of many industries that benefit from automated processes.
1. Aerospace
Given the immense size and scale associated with aircraft, the aerospace industry faces complex manufacturing requirements. Large components often require human operators and robots to work in tandem. In many cases, mobile robots that can travel between large aircraft parts are necessary to facilitate the process.
Moreover, robots can work in tight, hard-to-reach spaces, further enhancing productivity and quality. Automation minimizes the need for aerospace engineers to perform repetitive tasks, manipulate heavy objects, squeeze into tight spaces, and perform other hazardous processes while still adhering to critical quality standards.
Airplanes components have numerous holes that require drilling. Using special vision technology, robots can accelerate this drilling process while improving accuracy. Additionally, robots can assist and perform a wide variety of other tasks in assembling, preparing, inspecting and testing aircraft parts and components.
2. Medical Manufacturing
Given automation can perform tasks with fewer errors and higher precision, it’s an excellent tool for manufacturing, reporting, and documentation of medical devices and pharmaceutical products.
Automated medical device and implant manufacturing enhances quality control, assurance, and consistency. Using complex computing technology, cameras, and sensors, it provides accurate inspections, error detections, and automatic corrections. It also outputs and stores results for future reference, benefiting subsequent medical production processes and documentation for audits to maintain the highest industry standards.
While manual production requires constant slow-downs and stops for human evaluation, automation performs at high speeds, instantly detecting if a device is out of tolerance.
3. Automotive
In the automotive industry, robotics can lower human error in processes requiring automated reporting, manufacturing, and documentation. Their programmed safety features stop machinery when a worker gets too close, preventing a potentially serious accident.
Most automotive manufacturers use some form of automation at nearly every vehicle production stage. Tools like machine vision and robotics can perform a variety of tasks like welding, testing, inspection, and assembly. Automation improves safety, quality, and productivity in the automotive industry, completing more tasks in less time with minimal inaccuracies.
4. Packaging
Automation is a great way to increase packaging capacity. Robotic arms, for instance, are ideal for packaging applications due to their freedom of movement, high payload capacity, and ability to complete labor-intensive tasks in less time.
Manufacturers in the packaging industry can leverage technology to maintain a competitive advantage, product consistency, worker safety, and packaging flexibility for larger and more complex product varieties.
Best Automation Equipment and Systems
Various automation solutions can simplify different processes and tasks for manufacturing companies – from complete system automation to assisting certain processes. Some of these technologies include:
- Machine vision automation: Machine vision technology allows equipment to make quick decisions and verifications based on pre-programmed specifications. It’s ideal for visual inspections, part measuring and positioning, and defect detection. It can also assist in product identification, sorting, and tracking.
- Optical inspection automation: An optical inspection system can test defects in various parts, for example printed circuit board assemblies (PCBAs). A camera scans the device for scratches, stains, open circuits, shorts, missing components, improperly placed components, and much more.
- Robot arm automation: Robotic arms manipulate parts and products, which can be used for precise part placement/positioning in further processes, reducing human efforts for repetitive actions and difficult parts, and increasing safety.
- Robot inspection automation: Visual inspection robots feature complex vision sensors to inspect valuable or critical components, systems, and infrastructure.
- Cell controller automation/Cell inspection automation: An inspection cell is an enclosed unit or station dedicated to specific inspection tasks for given parts. Cell controllers are devices designed to coordinate, monitor, guide, and report part inspection processes, often linking multiple inspection cells. Through automated cell inspection a part can be accepted in an inspection cell, where an automated system can move around the object or precisely position it for a variety of tasks, including performing measurements, inspection, reporting, etc. The part can then be moved out of the inspection cell for additional processing. This level of manufacturing automation can achieve much higher throughput rates and greater gains in reproducibility, technical precision, and efficiency.
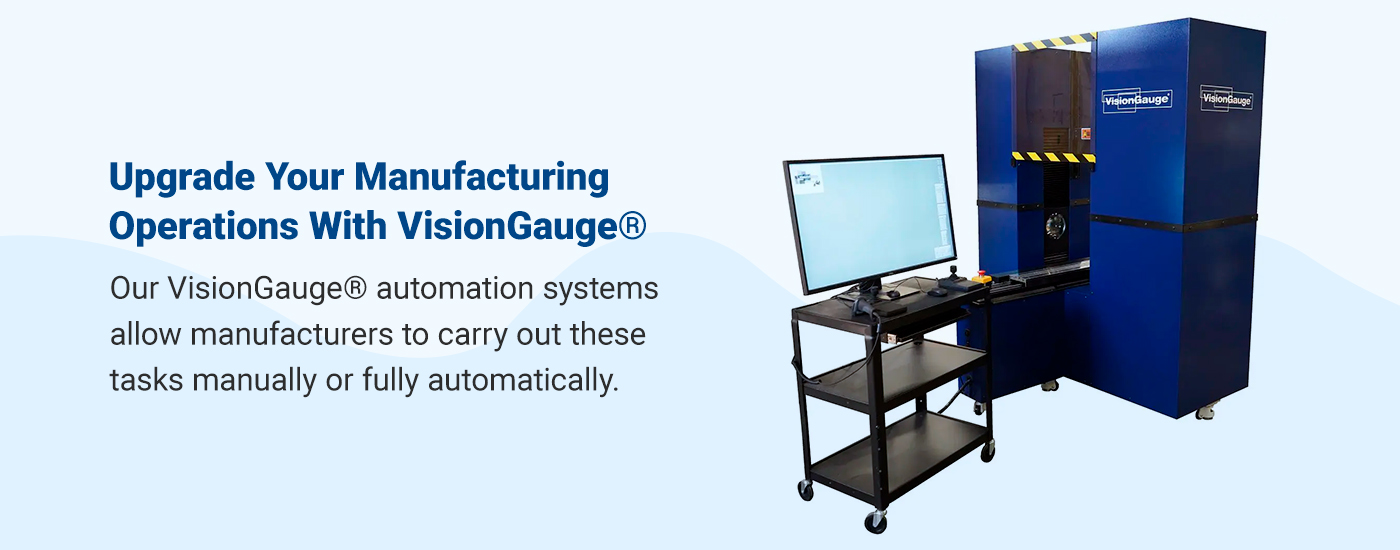
Upgrade Your Manufacturing Operations With VisionGauge®
At VISIONx, Inc., we develop software and equipment for complete visual part inspection, machine vision, image analysis, and defect detection to ensure they meet quality standards. Our VisionGauge® automation systems allow manufacturers to carry out these tasks manually-assisted or fully automatically. We have a wide variety of system types with many customizable options to solve applications across countless industries. Our VisionGauge® Digital Optical Comparator and our versatile Standalone Inspection and Measurement system are perfect to drop into any existing automated application.
These systems can perform various manual or programmed measurements and inspection operations, then collect and output data for streamlined reporting. They can easily interface with external equipment and machinery, such as cell controllers and robots – sending and receiving digital I/O signals or commands over a network. Furthermore, our VisionGauge® systems are incredibly simple to install and run.
If you’d like to invest in our advanced patented technology or learn more about our systems, reach out to our team today.